Significant savings with Proceedo when Norwegian salmon producer automated the procurement process.
Cost reductions and sustainability in focus for Bremnes Seashore using Proceedo
Bremnes Seashore
Big benefits from an automated purchasing process
Previously, Bremnes Seashore handled its purchasing and invoice management without any real structure. But after the Norwegian salmon producer automated the entire purchasing process with Proceedo, the benefits were huge - both in terms of money and climate savings.
NOK 14 million &
85% digital invoices
Mikael Søgaard, Procurement Manager at Bremnes Seashore, says that the company has made purchasing savings of NOK 14 million in 2020 compared to the previous year. In addition, the share of digital invoices has increased to 85%.
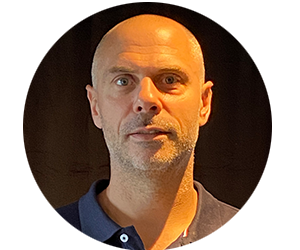
We have saved the equivalent of two full-time positions since we started working with Proceedo.
Mikael Søgaard
Procurement Manager, Bremnes Seashore
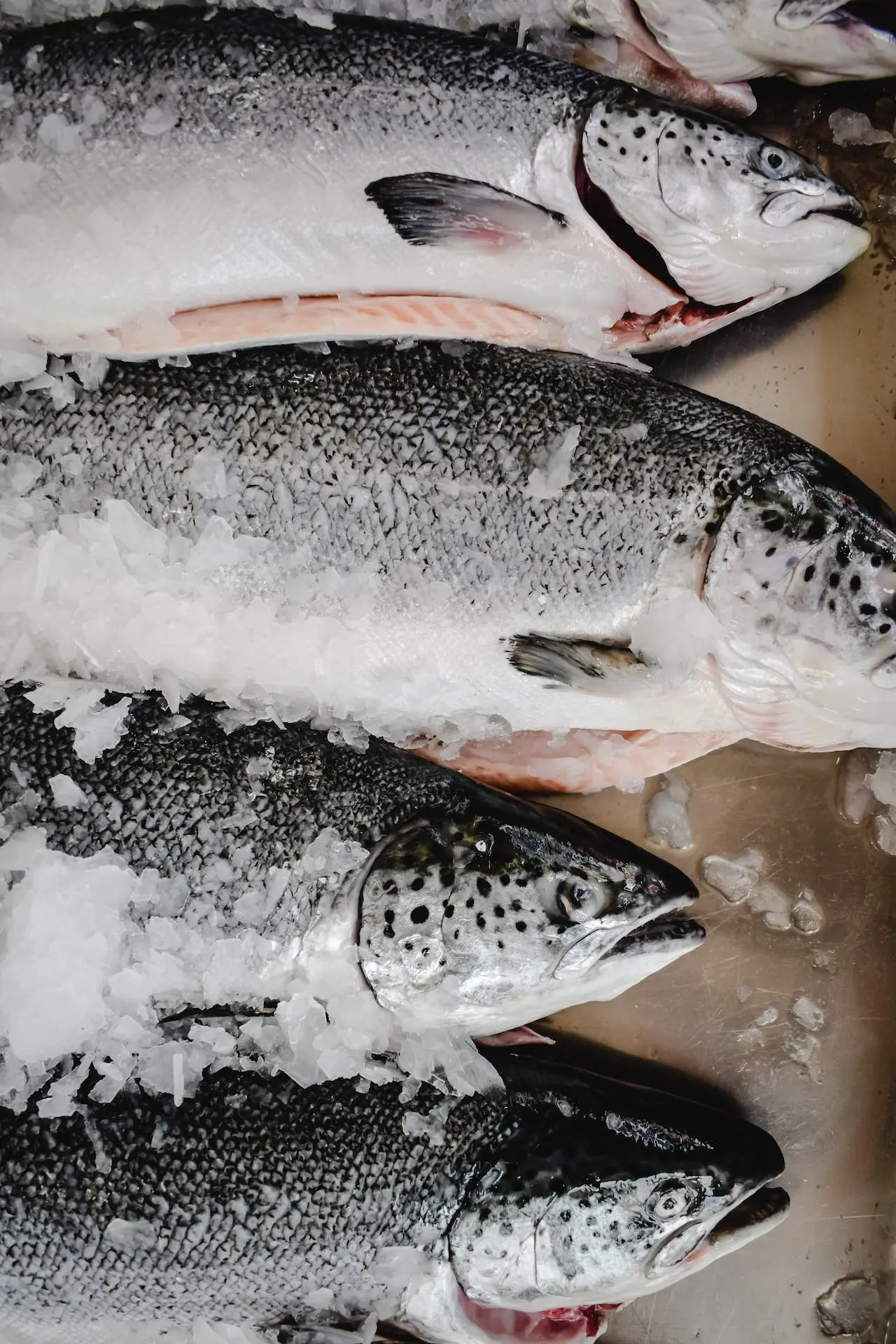
Bremnes Seashore
Bremnes Seashore is one of Norway's largest producers of salmon. With over 500 employees in around 30 cities, it's not hard to imagine that the purchasing and invoice management process is an extensive and significant part of the company's operations. Everything from fish feed to office supplies is purchased daily.
The company, which is behind the well-known Salmalax brand, has high climate and sustainability targets. Climate goals are important throughout the production chain, from the birth of the salmon to the exclusive fish fillets that end up in shops and restaurants across Europe. And the targets are equally high priority in procurement and invoice management.
Lacked a system with a simple interface for the end user
In the past, Bremnes did what many other companies did - it managed procurement and invoice management without any uniform structure, solutions that were time-consuming and labor-intensive. In addition, a large proportion of supplier invoices were sent by post in paper format and only a small proportion were digital e-invoices.
Bremnes needed to find a simple and uniform solution for its purchasing process. According to Mikael Søgaard, Procurement Manager at Bremnes Seashore, there were several key requirements that had to be met. Such as a simple interface for the end-user, a proactive and experienced system provider with great expertise and good terms.
The solution was Proceedo with smooth and user-friendly digital solutions and with long experience in simplifying the purchasing and invoice management process for companies and organizations. With this automated process from order to payment, it is easy to buy the right goods at the right price.
Big savings on purchases
Today, the entire corporate group is integrated into Proceedo's Purchase-to-Pay solution. Bremnes has gained a holistic view of its suppliers and costs and a complete insight into and control over all parts of the processes. And procurement manager Mikael Søgaard sees several major benefits.
- "When it comes to invoice management, we have saved 2 full-time positions since we started working with Proceedo's system. Previously, it took an average of 8.5 days to process an invoice, today it takes 5.2 days, he says.
- The proportion of digital invoices has also increased from 35 to 85 percent, which is obviously a big win considering the climate impact of sending invoices by letter, says Mikael Søgaard.
Before we started using Proceedo services, we had low contractual compliance. Today it is twice as high.
Mikael Søgaard
Procurement Manager, Bremnes Seashore
Increased invoice matching
Other examples of concrete savings Bremnes made with Purchase-to-Pay in 2020 compared to 2019 are:
- More than 60 new contracts have been signed.
- The processing time for each invoice has been reduced by 2.8 days to 5.0 days.
- Invoice matching has increased from 44 to 66 percent.
Proceedo is also smooth and easy to use, a very important factor according to Mikael Søgaard.
- "Previously, we had a difficult interface in the system for invoice management. Today we have a much more user-friendly interface," he says.
Increased contractual compliance
In addition to saving time and improving agility, contractual compliance with suppliers has doubled. Buying from suppliers with whom you already have a contract obviously offers better conditions, such as lower prices and discounts, compared to "spontaneous buying" from many different suppliers. In 2020, the number of suppliers was reduced by 19 percent compared to 2019, a figure that indicates that you are on the right track.
- "Before we started using Proceedo, we had a low contractual compliance. Today, it is twice as high and the goal is to reach 100 percent," says Mikael Søgaard.
Climate-smart invoices
On Mikael's wish list when it comes to future procurement and invoice management, climate and sustainability are in focus, to develop the already great benefits of Proceedo Purchase-to-Pay even more in the long run. He has thoughts about CO2 and about being able to "earmark" the amount of climate impact on each individual shipment to know exactly how each processed invoice affects the climate and the environment.
- Bremnes Seashore aims to minimize the climate impact of all our activities. If we can see, for example, how much CO2 emissions each invoice causes, we have reached another important goal," says Mikael Søgaard.
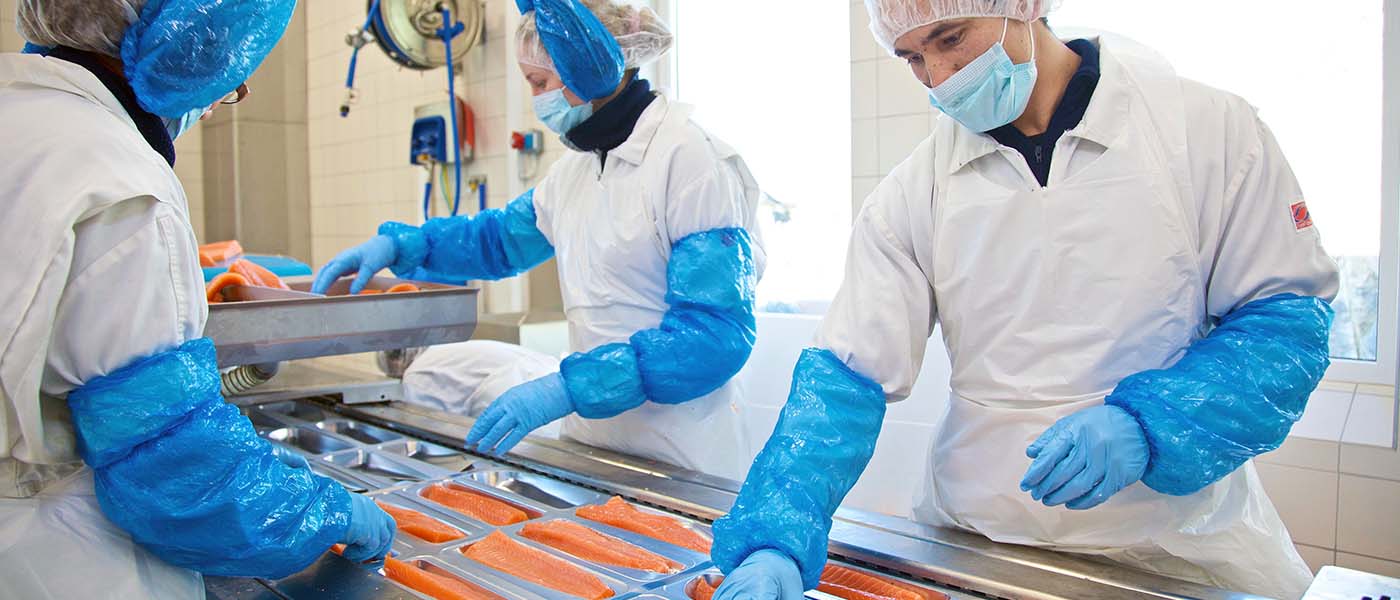
Fact box
Bremnes Seashore
Capacity: Bremnes Seashore produces 200-300 tons of salmon per day, equivalent to 12-18 full trailers.
Turnover: NOK 2 359 million.
Number of employees: About 500 in 30 cities and towns.
Founder: Olav Svendsen started receiving seaweed and kelp on the quays at his home in Øklandsvågen in 1937 at the age of 14. Today, his descendants still run the company.
Head office: In Øklandsvågen in Bømlo municipality, the same place since the start in 1937.
Environmental work: Bremnes Seashore has high environmental and sustainability goals. Clean seawater and access to raw materials for fish feed are the foundation of the business. As much as 98% of the fish product is recycled.
Best-known product: Salmalax , which was chosen as Product of the Year 2013 at the grocery gala organized by the magazine Fri Köpenskap.